Product Description
The FFI Welding Electrodes Production Line Plant is designed to meet the increasing demand for high-quality welding electrodes in the manufacturing industry. This versatile equipment is capable of producing a wider ranges of welding electrodes, from standard mildly steel to advancing alloy varieties.
The FFI Welding Electrodes Production Line Plant is perfect for businesses looking to produce welding electrodes in-house, instead of relying on expensive third-party suppliers. With this equipment, you can produce up to 10 tons of welding electrodes per day, making it ideal for large-scale productions.
The FFI Welding Electrodes Production Line Plant is made of high-quality resources and is particularly intended to produce functionality this is certainly constant small recovery time. The cutting-edge innovation permits exact command over manufacturing procedures, making sure every electrode happens to be of top quality and matches the strictest market criteria.
The FFI Welding Electrodes Production Line Plant is simple to run, actually for everyone with restricted knowledge in welding electrode creation. Their control which is user-friendly board the agent to supervised and readjust manufacturing procedures quite easily, making sure that the apparatus runs at optimum performance.
The FFI Welding Electrodes Production Line Plant works with a selection of welding electrode preparations, permitting companies to generate a array this is broad of for a variety of apps. This adaptability helps to makes the FFI Welding Electrodes Production Line Plant an decisions that is definitely great organizations aiming to broaden what they are offerings choices and grow their unique client base.
The FFI Welding Electrodes Production Line Plant is designed with safety in mind. All moving parts are enclosed, and the equipment is equipped with safety features, such as emergency stop buttons and automatic shut-offs in case of malfunction. This ensures that both the operators and the equipment are protected from harming.
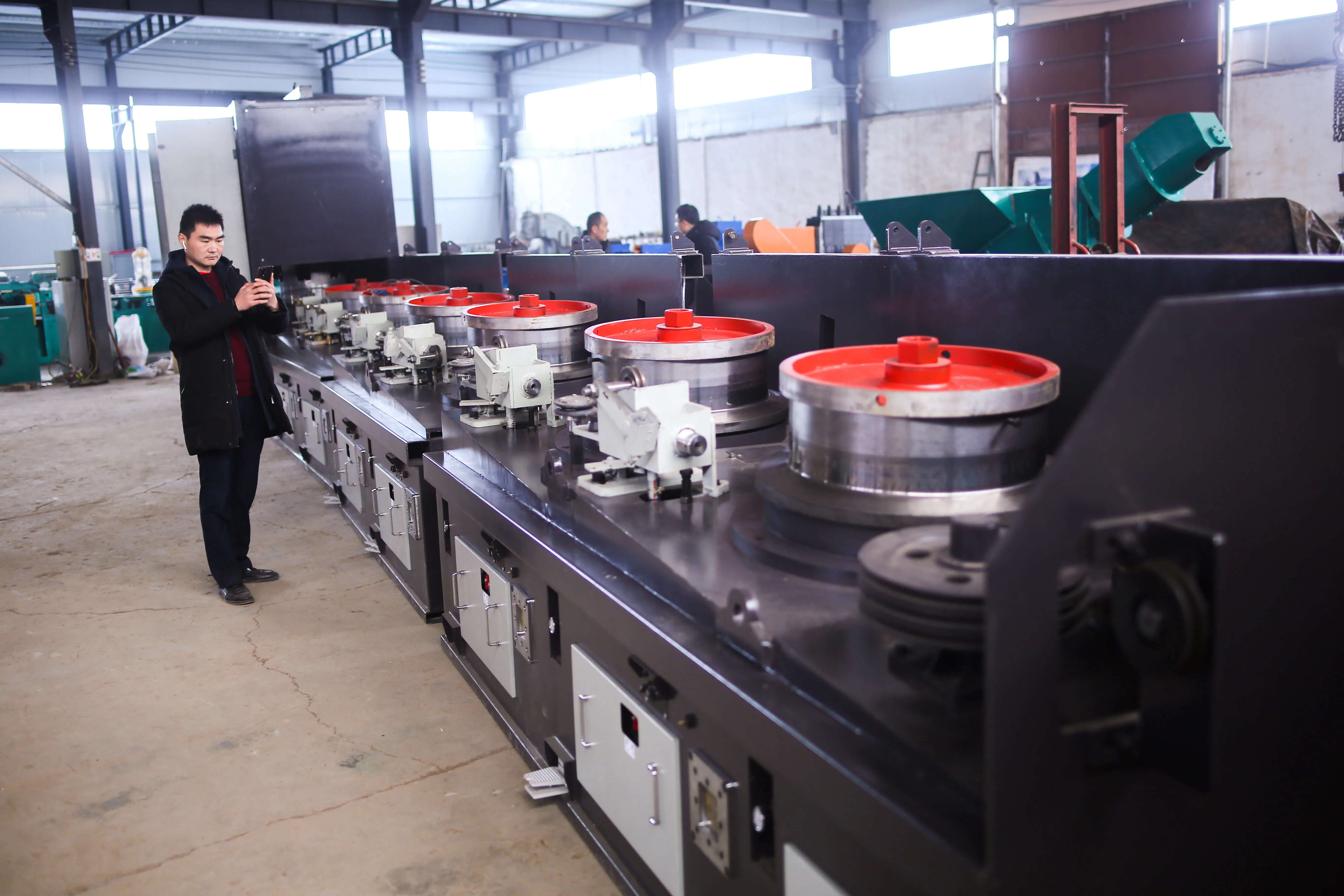
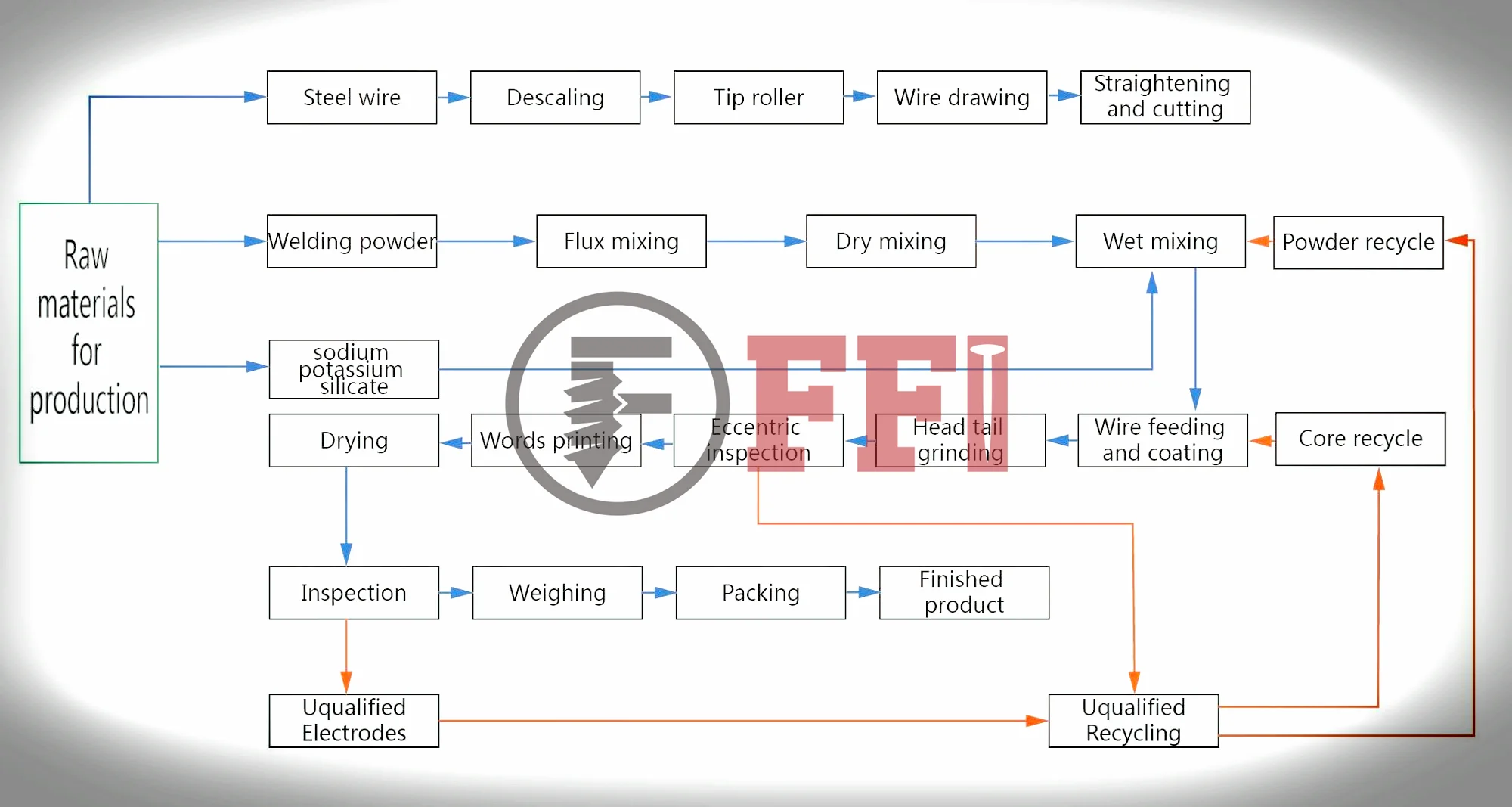
No. |
Equipment |
Function |
1 |
Descaling machine |
Remove the dust from the wire. |
2 |
Tip roller |
Sharpen the tip of wire. |
3 |
Butt-welding machine |
To weld the wire tips when 1 roll is finished. |
4 |
Wire drawing machine |
To draw the wire into diameter needed. |
5 |
Single arm crane |
To lift the wires. |
6 |
Wire cutting machine |
To cut wire into size. |
7 |
Powder mixer |
Mix the powder for coating. |
8 |
Wire-feed machine |
Wire supply. |
9 |
Helix powder coating machine |
Coat the mixed powder onto the wire. |
10 |
Head-Tail Grinder machine |
To grind the head and tail into standard shape. |
11 |
Electrode eccentric measuring Instrument |
Eccentric checking. |
12 |
Control panel for spiral line |
Main control of electricity. |
13 |
Auxiliary line machine |
Internal conveying. |
14 |
Box type hot air circulation drying furnace(electricity) |
Drying the coating on the core. |
15 |
Words printer |
Printing dates or brand name. |
16 |
Shrink packaging machine |
Plastic packing. |
17 |
Strapping machine |
Wrapping. |
18 |
Reclaiming machine |
Peel the coating off. |
19 |
Straightening machine |
Straighten the wire. |
20 |
Vibrating screen |
To filter the recycled coating. |

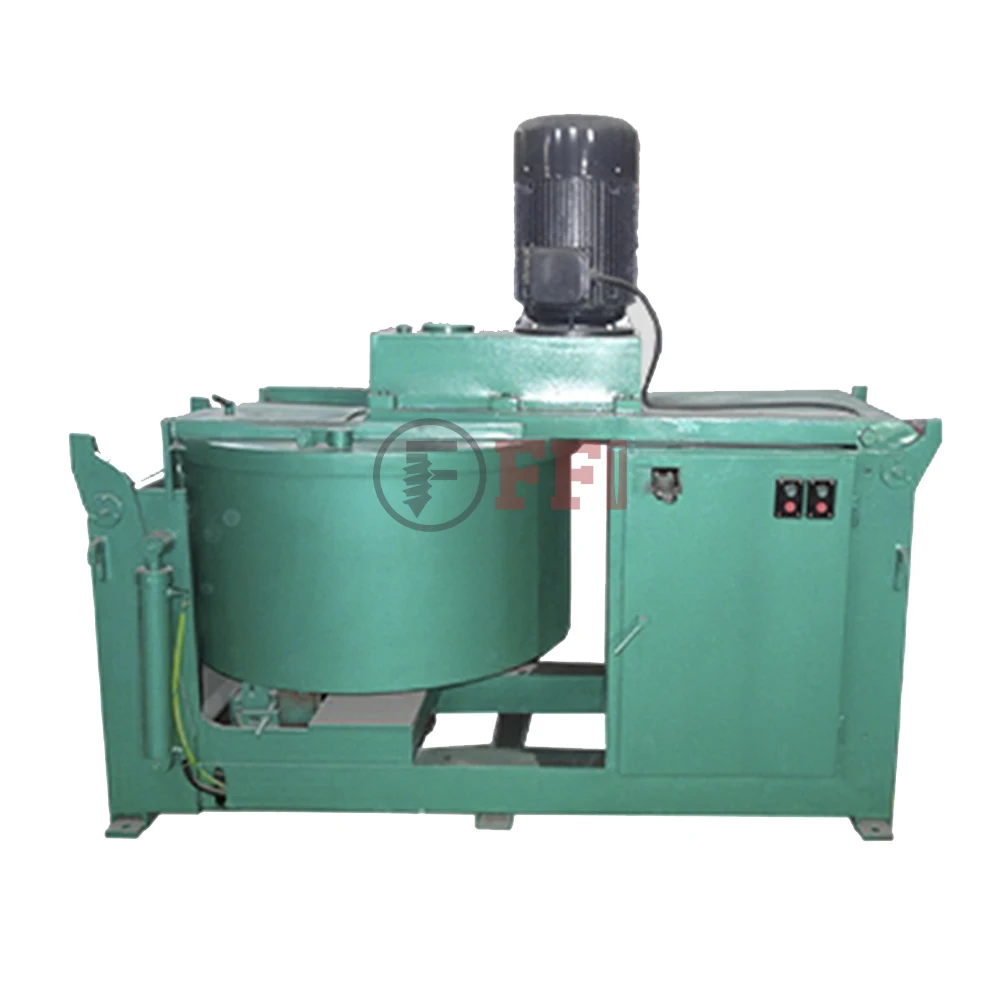
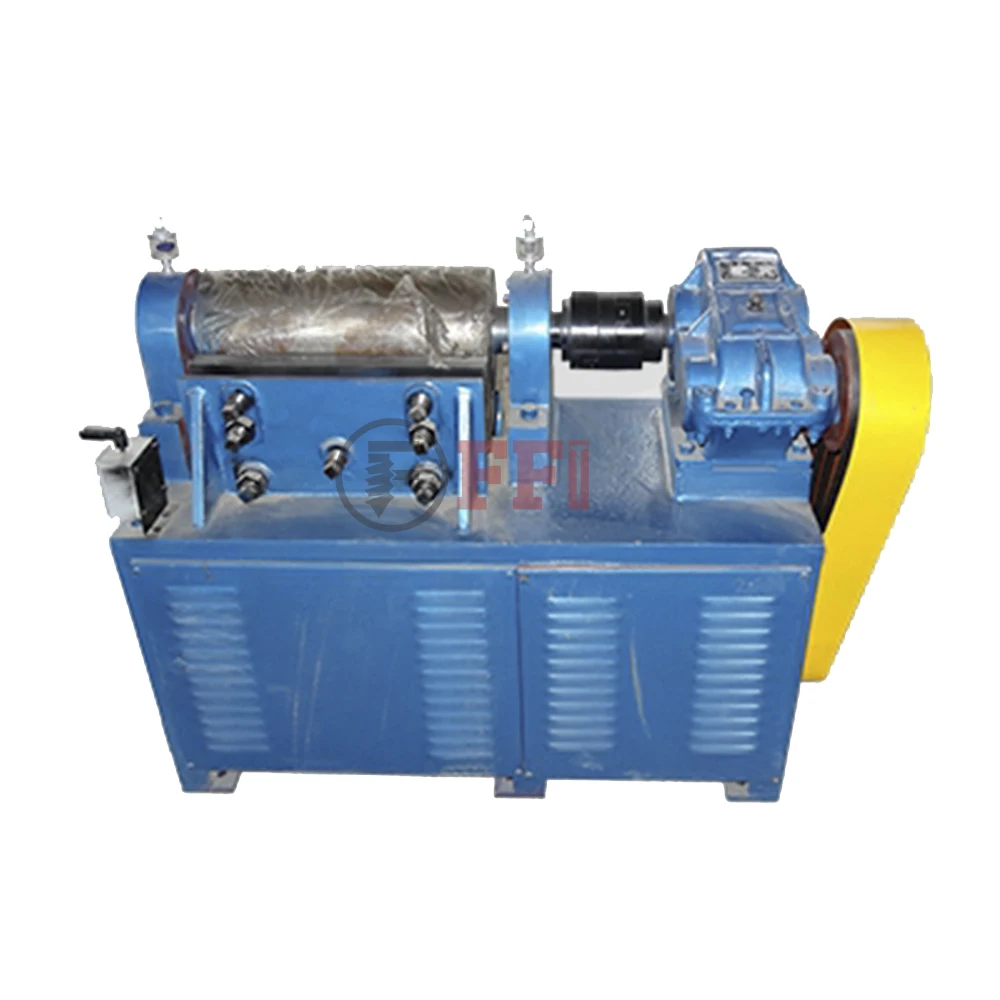
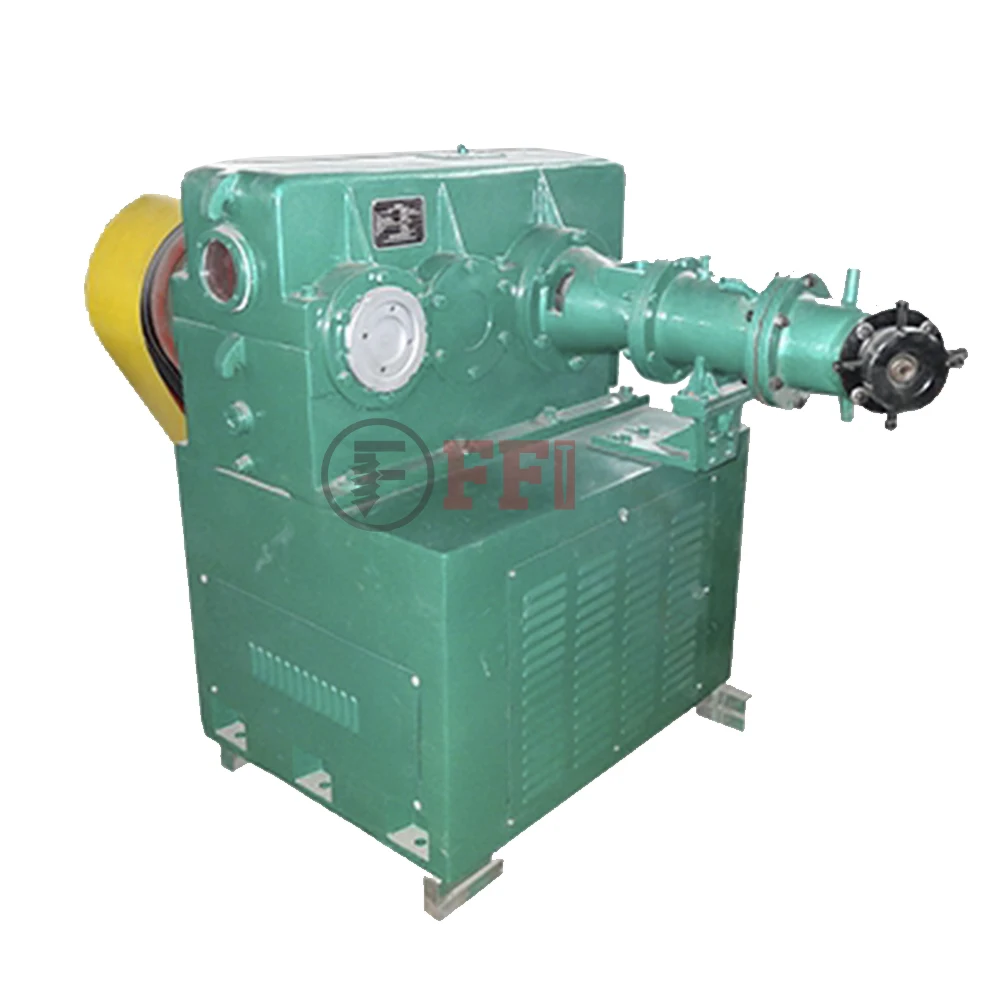
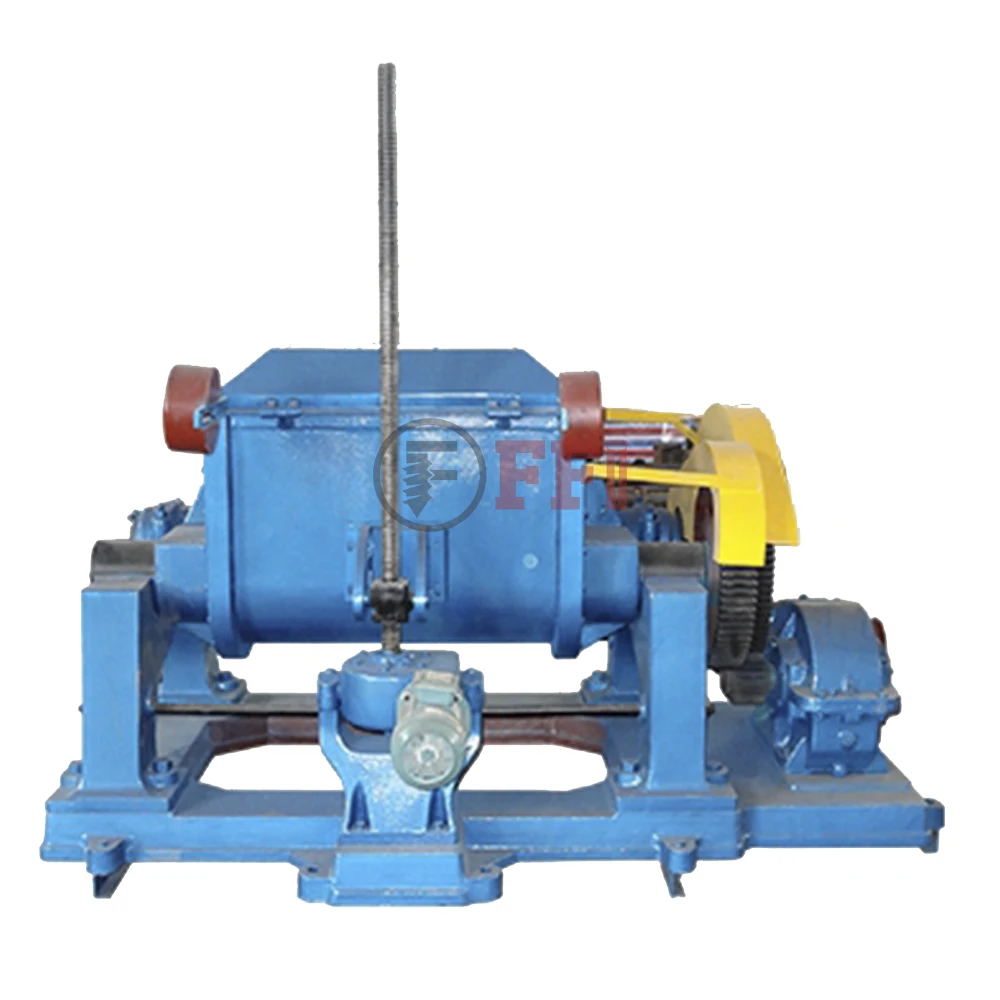
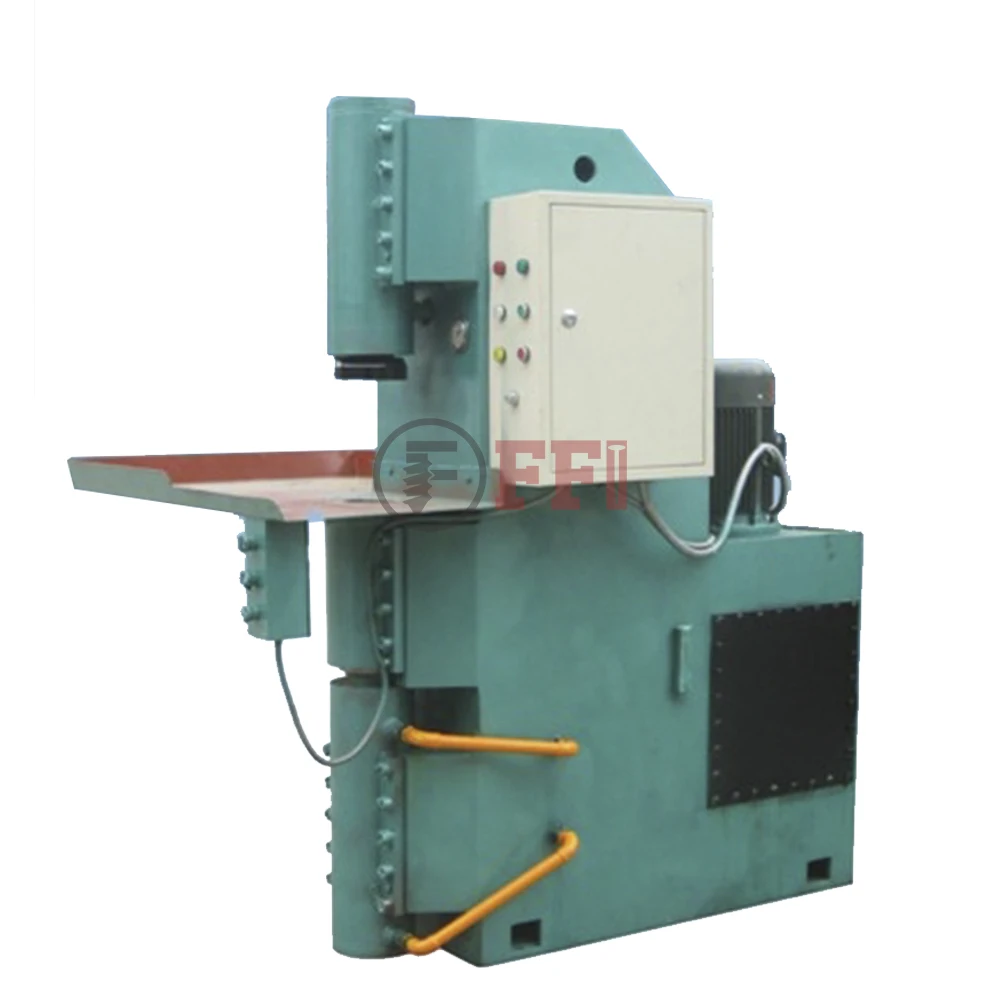
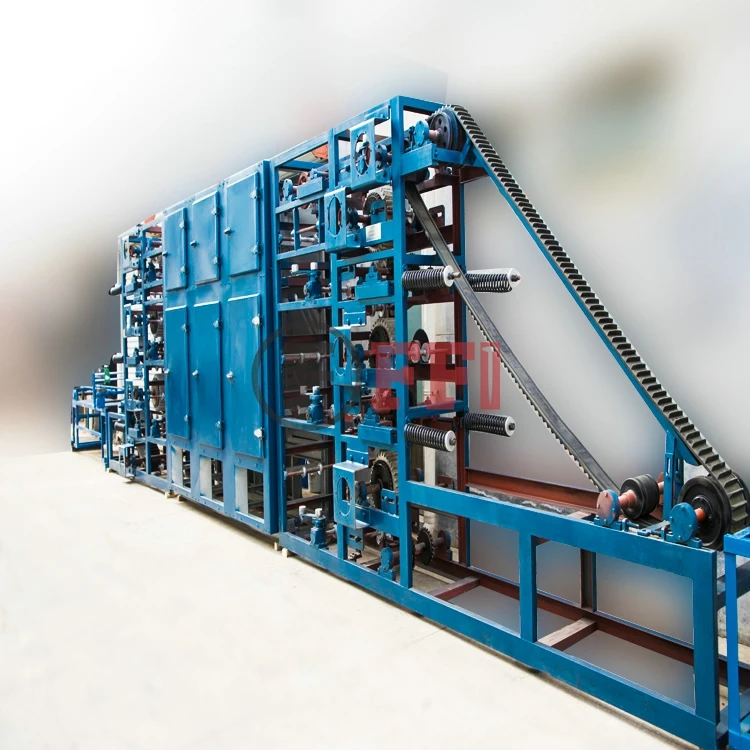
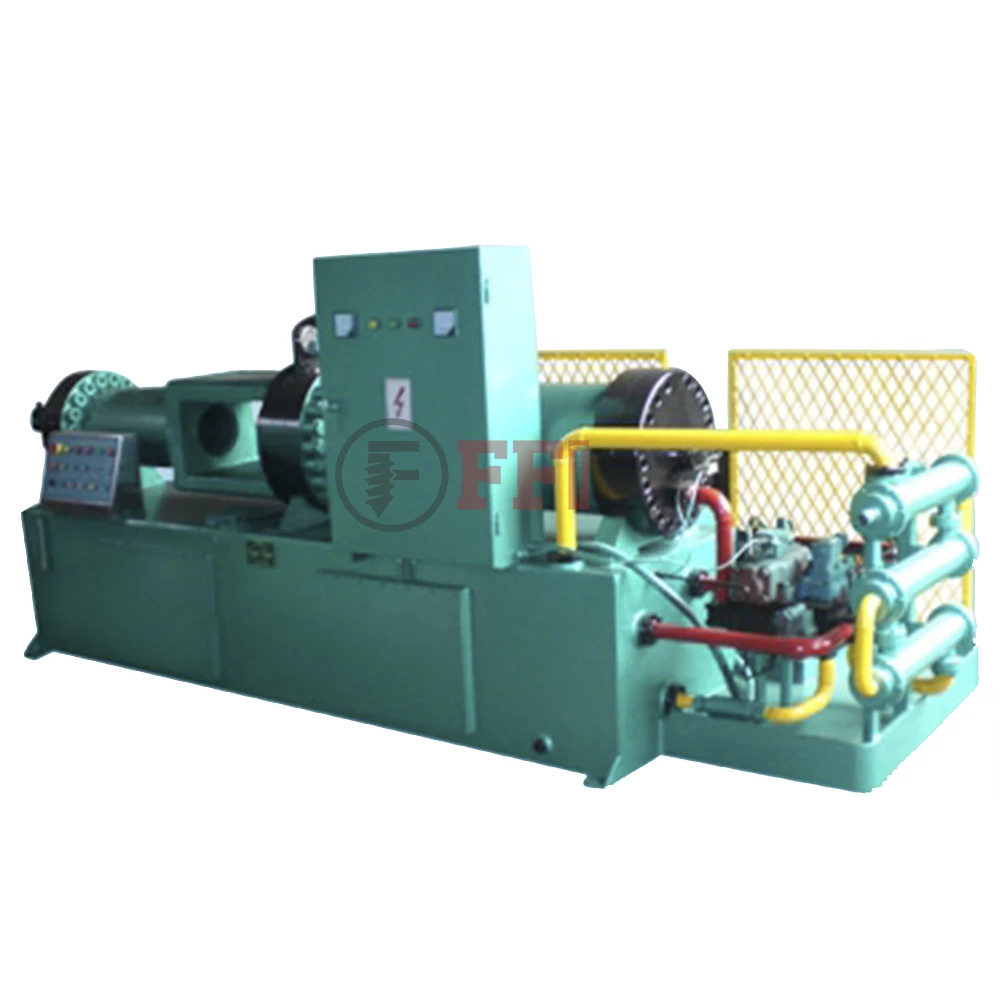
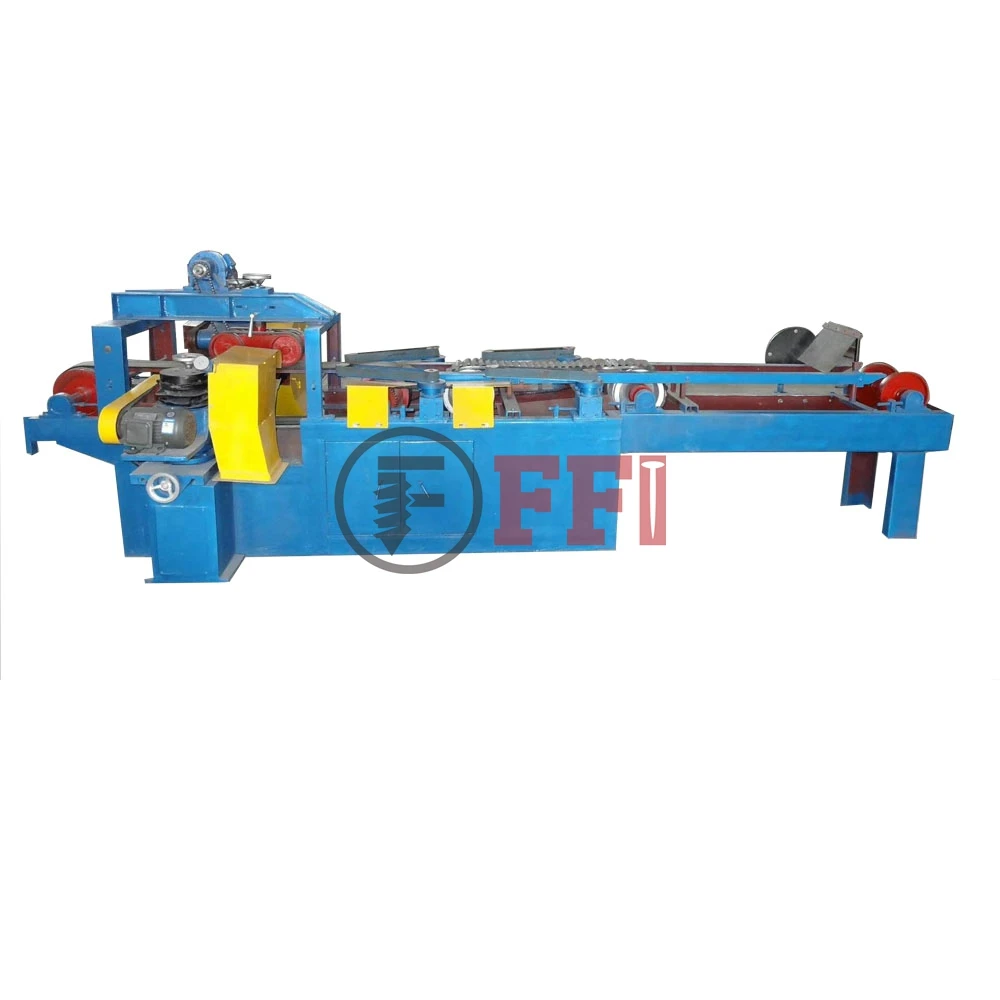